Overview Research Facilities Team Data News Publications Newsletter Contact
More than 25 years after their commercialization, lithium-ion batteries still continue to pose reliability and safety challenges. While the research has enabled the discovery of high-performance battery materials and advanced the fundamental understanding of their electrochemical characteristics, the link between fundamentals and cell/pack level electrical characteristics and long-term performance remains weak. We at CALCE are working to establish and develop this link to allow the utilization of lithium-ion chemistry to its true potential while ensuring its reliability and safety. We have been supported in our efforts by US NAVY, NASA, US Army, DOD, NSF, and many industries including Dell, HP, GE, Honeywell and IBM over the years. Our current and past research projects are summarized as follows:
Exploration of Novel Accelerated Testing Conditions for Qualifying Li-ion Batteries
Life testing of Li-ion batteries is conducted for qualification purpose by assessing its capacity fade based on the requirements for its targeted application. However, testing at normal operating conditions can be quite time-consuming. To identify highly accelerated testing methods, CALCE has been collaborating with two major consumer electronics manufacturers and 6 of the world’s largest battery manufacturers. While the effects of temperature on accelerated degradation of Li-ion battery performance have been studied and modeled in the literature, the combined effects of discharge C-rate with other factors still require deeper understanding.
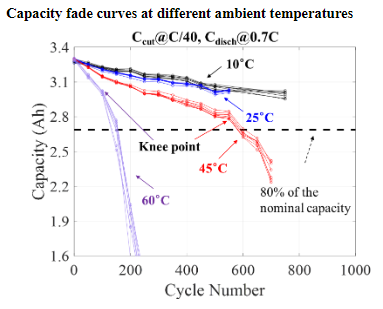
References: Accelerated Cycle Life Testing and Capacity Degradation Modeling of LiCoO2-graphite Cells , Weiping Diao, Saurabh Saxena, and Michael Pecht, Journal of Power Sources, Vol. 435, September 2019, DOI: 10.1016/j.jpowsour.2019.226830.
Accelerated Degradation Model for C-rate Loading of Lithium-ion Batteries, Saurabh Saxena, Yinjiao Xing, Daeil Kwon, and Michael Pecht, International Journal of Electrical Power & Energy Systems, Vol. 107, pp. 438-445, May 2019, DOI:10.1016/J.IJEPES.2018.12.016.
Thermal Runaway Characterization of Li-ion Batteries
Investigation of Tab Design and Failures in Cylindrical Li-ion Batteries
Lithium-ion (Li-ion) batteries have powered today’s portable and rechargeable products, and the cylindrical format is widely used in applications ranging from e-cigarettes to electric vehicles. The tabs in these batteries connect the electrodes (current collectors) to the external circuits. Li-ion battery failures such as fires and explosions can be caused by manufacture defects, especially associated with tab defects such as welding burrs and improper tab locations. The electrode tabs are the metallic strips that are welded onto the current collectors without active materials. When the battery is charged or discharged, the temperature around the electrode tabs is higher than other places inside the cell due to the high current density. CALCE is studying the effect of tab design and placement on battery reliability and safety.
References: Tab Design and Failures in Cylindrical Li-ion Batteries, Xing-Yan Yao, and Michael Pecht, IEEE Access,, Vol. 7, pp. 24802-24095, February 15, 2019, DOI: 10.1109/ACCESS.2019.2899793.
Partial State of Charge (SOC) Cycling Effects on Capacity Fade of Lithium-ion Cells
In practical applications, batteries may undergo charge-discharge cycling only for partial SOC ranges as opposed to the full 0%–100% range. CALCE has been performing cycle life testing of commonly used graphite/LiCoO2 pouch cells in different SOC ranges (e.g., 0-100%, 20-80%, 20-100%) to understand the effects of different SOC ranges on battery capacity fade and to model the battery capacity fade as a function of mean SOC, ∆SOC and cycle count. The developed models can be used for battery health management in field applications as well as for accelerated testing during battery qualification.
SOC ranges during cycling affect degradation mechanisms such as SEI layer formation and crack generation in the electrode. For example, as we increase the upper limit of SOC (end of charge voltage) in cycling, the amount of lithium in the anode increases, resulting in anode lattice volume expansion and causing localized stress. Also continuous cycling with higher ∆SOC value increases the probability of crack generation in the anode due to cyclic fatigue. These cracks in the anode provide fresh sites for electrolyte reduction and SEI layer growth, causing loss of cycleable lithium and higher electronic resistance. The figure below shows the effect of lowering the ∆SOC on the battery degradation.
Reference: Cycle life testing and modeling of graphite/LiCoO2 cells under different state of charge ranges, Saurabh Saxena, Christopher Hendricks, and Michael Pecht, Journal of Power Sources, Vol. 327, pp. 394-400, September 2016.
Management of Imbalances in Parallel-connected Lithium-ion Battery Packs
Uneven electrical current distribution in a parallel-connected lithium-ion battery pack can result in different degradation rates and overcurrent issues in the cells. Understanding the electrical current dynamics can enhance configuration design and battery management of parallel connections. This study presents an experimental investigation of the current distribution for various discharge C-rates of both parallel-connected LiFePO4 and Li(NiCoAl)O2 cells. A first-order Thevenin model for current distribution calculation was applied to assess the maximum discharge current discrepancy between cells when the number of cells increases. This study reveals why balancing circuits are seldom implemented on cells in a parallel connection, and provides guidance on reducing cell imbalances by managing battery operation in terms of state of charge range and discharge C-rates, as well as improving connection design.
Reference: Management of imbalances in parallel-connected lithium-ion battery packs, Diao, W., Pecht, M., & Liu, T., Journal of Energy Storage, Vol. 24, 2019, 100781.
Physics-based Electrochemical Model for Lithium-ion Battery State-of-charge Estimation
As electrochemical models can accurately simulate battery behaviors with the entire scope of state of charge (SOC), they are very appealing in BMS. However, the large computational cost of solving partial differential equations limits their practical applications. On account of low computational cost, simplified electrochemical models are more suitable. A simplified electrochemical thermal coupling model with reduced and regrouped model parameters was established and a method for nondestructive parameter estimation for individual cells was developed based on excitation response analysis. The parameters were classified into two categories: inherent characteristic parameters and mechanistic parameters. Inherent characteristic parameters could be obtained by consulting manufacturers directly or measuring. Mechanistic parameters were obtained by the excitation response analysis. According to different response time of different processes in the developed model when a cell was applied with different current excitations, the corresponding parameters were then obtained by least square fit.
To solve the computationally complex solid-phase diffusion partial differential equations (PDEs) in the model, CALCE developed an efficient method based on projection with optimized basis functions and a novel moving-window filtering (MWF) algorithm to improve the convergence rate of the state filters.
Reference: A Physics-Based Electrochemical Model for Lithium-Ion Battery State-of-Charge Estimation Solved by an Optimised Projection-Based Method and Moving-Window Filtering , Wei He, Michael Pecht, David Flynn, and Fateme Dinmohammadi, Energies, Vol. 11, No. 2120, pp. 1-23, 2018, DOI: 10.3390/en11082120.
Electrochemical Characterization of Lithium-ion Batteries Using a Three-electrode System
Recently, Lithium-ion batteries have been used in many electronic devices including laptops, smartphones, electric vehicles (EVs) and are also being considered for military and space applications. Generally, (commercial) Li-ion batteries have two-electrode. Therefore, the battery voltage or impedance can be measured only across the negative and positive electrode. In order to understand the fundamental electrochemical characteristics and to utilize the Li-ion battery chemistry more efficiently and safely, it is of interest to study the performance of each electrode separately. A three-electrode system is able to interpret the electrochemical characteristics of the individual electrodes. A widely used commercial 18650 battery (LiFePO4/ graphite) was reconstructed into a three-electrode full cell. Based on the three-electrode cell, the voltage and impedance of not only the full cell but also the individual electrodes were monitored. Accordingly, the electrochemical behavior of the commercial cell was explained and the contribution of each electrode to the full cell was identified.
Dendrite Formation Mechanism
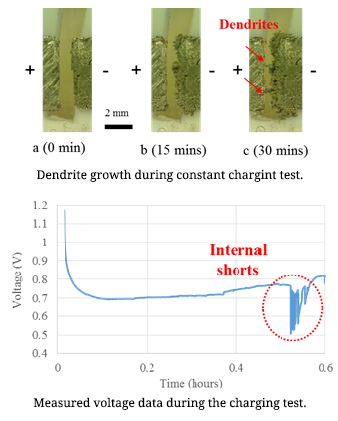
In order to increase Li-ion battery safety, it is necessary to conduct research on lithium dendrite formation mechanism. For this purpose, an in-situ observation method was used to detect dendrite formation at various current densities and temperatures. The relationship between the applied current density and the dendrite growth rate is the research focus in the first step of study. In order to determine the dendrite growth rate, a symmetrical lithium cell (both the positive and negative electrodes were made of lithium metal) was charged at constant current. The developed in-situ testing method can be used for identification of dendrite formation inside cells. Battery safety operation boundary conditions can be determined using this work.
Reference: In-situ Observations of Lithium Dendrite Growth, Lingxi Kong, Yinjiao Xing, and Michael Pecht, IEEE Access, Vol. PP, Issue 99, February 21, 2018, DOI: 10.1109/ACCESS.2018.2805281.
Ultrasonic Health Monitoring of Lithium-ion Batteries
Reference: Ultrasonic Health Monitoring of Lithium-Ion Batteries , Yi Wu, Youren Wang, Winco K.C. Yung, and Michael Pecht, Electronics, Vol. 8, No. 751, DOI: 10.3390/electronics8070751.
Battery Management System (BMS) Research
CALCE is dedicated to developing a BMS that not only assures safe usage, but also provides the most reliable performance and operational battery health information.
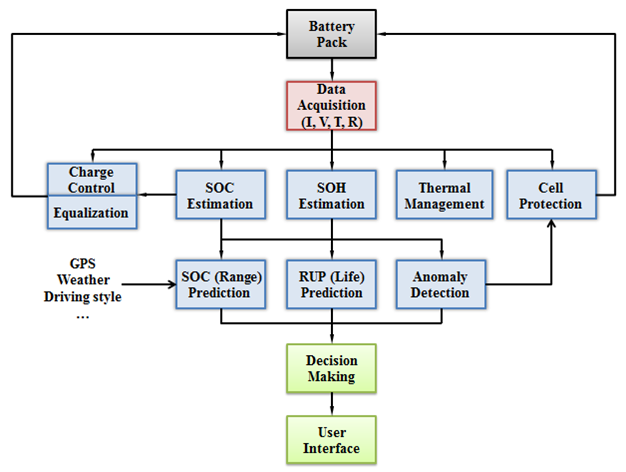

Top