News Story
Professor Dasgupta and Students Present at ASME IMECE Conference
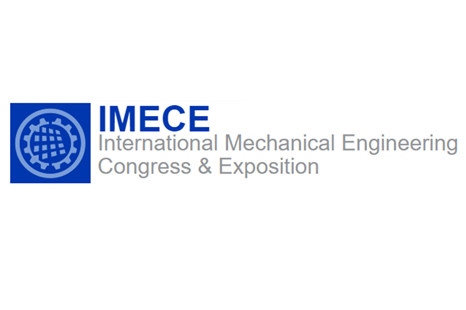
At the conference, Prof. Dasgupta attended the Design Materials and Manufacturing Segment Leadership Team and co-chaired the inaugural symposium ‘Constitutive Modeling of the Mechanical Behavior and Performance of Electronic, Photonic, MEMS, and NEMS, Materials, Assemblies, Packages, Modules, and Systems,’ which was organized by the Applied Mechanics and Materials Divisions.
Abstract for Hao Huang’s ‘Constitutive Model for Pressure-Sensitive Adhesive (PSA) Joints’
The challenges of modeling the deformation of structures containing pressure sensitive adhesive (PSA) joints includes: a) the dependence of the PSA deformation mechanism on the bonding substrate’s surface properties, such as surface energy and surface roughness; and b) multiple transitions in their stress-strain and creep curves. These transitions are evidenced by a sudden drop in the stress level (under constant strain-rate) in the stress-strain curve and by a sudden increase in creep strain rate (under constant stress level) in the creep curve. In this paper, a mechanism-based predictive model is presented for generating the constitutive behavior of complex uniaxial stress-strain and creep responses of a single-layered PSA joint. The model is based on multiple mechanisms: (i) cavity nucleation and growth in bulk PSA and at the interface between the PSA and the substrate; (ii) fibrillation of the adhesive layer; and (iii) interfacial slippage between the adhesive and the bonding substrate. This study is motivated by the fact that the conventional constitutive models currently available in commercial FEA tools are not adequate to describe the complex nonlinear mechanical behavior of PSA joints. Additionally, the current mechanistic models in the literature are insufficient to make reasonable predictions of the stress-strain and creep responses of PSA joints. The proposed model is based on the ‘block’ model for single-layered PSA. Stress-strain and creep curves generated by the predictive model can be used as constitutive models for PSA joints when using commercial FEA tools, such as ABAQUS or ANSYS, for assessing the deformation of structures containing single-layered PSA joints under different loading conditions.
Abstract for Qian Jiang’s ‘Anisotropic Hill Constants for Steady-state Creep Behavior of Single SnAgCu Joints Based on Multi-scale Modeling’
Tin-based solder alloys usually experience high homologous temperature because of their relatively low melting temperature. Therefore, time-dependent creep deformation at elevated temperature has a significant effect on the performance and reliability of solder joints. SnAgCu (SAC) solder used in microelectronics commonly have a coarse-grained microstructure and the strongly anisotropic properties of the Sn phase render each SAC grain’s behavior highly sensitive to its orientation. Thus, SAC interconnections often exhibit wide piece-to-piece variability, based on the grain structure of each joint. Computational simulation of coarse-grained joints requires suitable anisotropic continuum creep models such as Hill’s model for capturing the behavior of each grain. This model requires six model constants that are usually obtained from difficult creep experiments along the different crystal directions. An alternative is to use predictive virtual-testing models to theoretically estimate the six anisotropic Hill constants. A multi-scale anisotropic model has been proposed by the authors to enable this virtual testing prediction of the six Hill constants from simulated steady-state creep behavior of single SAC crystal, according to its microstructure. Each grain is modeled as pro-eutectic Sn dendrites surrounded by eutectic Sn-Ag phase, where the eutectic Sn-Ag phase is simulated as nano-scale Ag3Sn IMC particles dispersed in Sn matrix. The creep behavior of the eutectic phase is modeled with dispersion strengthening mechanisms, using dislocation mechanics formulations. The load sharing between the eutectic phase and the dendritic ?-tin phase is modeled with two-phase composite homogenization methods. Examples are presented, using a commercial FEA code, to illustrate this virtual testing approach. Simulation results are compared with experiments to validate the method.
More information about the International Mechanical Engineering Congress & Exposition can be found here.
Published November 19, 2018