Standards act as a bridge between academic knowledge and industry applications. Standards translate complex academic research and theoretical concepts into practical, step-by-step guidelines, making knowledge more accessible and readily usable for engineers and technicians working in the field. Standardization bodies often include academics and industry experts. By working together, they can create standards that use consistent terminology and address industry needs while incorporating the latest research findings, creating a common language for researchers and industry professionals to communicate and collaborate.
Companies can validate academic research findings by testing and developing products that meet these standards. In turn, the successful implementation of academic ideas in industry standards can further validate the research itself. The process of developing standards often involves identifying industry problems and then researching solutions. Academics can contribute their knowledge and research to inform these discussions, ultimately leading to standards that address real-world industry challenges.
Standards themselves may not directly contain all the intricacies of academic research. However, they act as a bridge, pointing industry professionals toward the underlying research and its detailed findings.
Overall, standards play a crucial role in facilitating the transfer of academic knowledge to the electronics industry by providing a common language, codifying knowledge, and establishing frameworks for problem-solving and validation.
There is always a time lag between cutting-edge academic research and its incorporation into industry practices. By leading in the development and adoption of standards, CALCE researchers have helped lower that gap.
CALCE research has directly resulted in the contents of several standards. These include IEEE 1624, IEEE Standard for Organizational Reliability Capability, IEC TR 62240-1, Process management for avionics - Electronic components capability in operation - Part 1: Temperature uprating, SAE GEIASTD0005_1B, Standard for Developing a Lead-Free Control Plan to Manage the Risks of Lead-Free Solders and Finishes in Aerospace, Defense, and High-Performance Soldered Electronic Products.
CALCE made one of the most substantial early pushes for standardization in the area of reliability programs and prediction. Governments and industries use the standards that came out of those efforts. Some of those standards include IEEE 1332-2012, IEEE Standard Reliability Program for the Development and Production of Electronic Products, IEEE 1413, IEEE Standard Framework for Reliability Prediction of Hardware, IEEE 1413.1, IEEE Guide for Selecting and Using Reliability Predictions Based on IEEE 1413, and IEEE 1624, IEEE Standard for Organizational Reliability Capability. Currently, updates are underway on these standards, led by Dr. Diganta Das and Dr. Michael Azarian. In addition, Dr. Diganta Das serves as the vice chair of the IEEE Reliability Society’s standards association.
The counterfeit avoidance and detection standards being developed under the auspices of the SAE Aerospace Council are benefiting from the expertise and leadership of CALCE researchers. CALCE has participated in and helped include best practices in various published and in-development SAE standards. The imprints of CALCE work are demonstrated in the SAE G19 developed supply chain level standards SAE AS5553 Counterfeit Electronic Parts; Avoidance, Detection, Mitigation, and Disposition, SAE AS6081 Counterfeit Electrical, Electronic, and Electromechanical (EEE) Parts: Avoidance, Detection, Mitigation, and Disposition - Independent Distribution, and SAE AS6496 Fraudulent/Counterfeit Electronic Parts: Avoidance, Detection, Mitigation, and Disposition - Authorized/Franchised Distribution.
The most significant contribution to the SAE counterfeit standards space came in the area of detection of counterfeit electronic parts. Dr. Michael Azarian chairs the SAE G19A committee which shepherds this suite of standards. The standard is implemented when other risk mitigation methods for avoiding the use of suspect/counterfeit EEE parts (e.g., acquiring all parts from authorized sources, redesigning the system, having obsolete parts emulated) are either unavailable or inadequate. There are 16 test methods standards associated with the main document of the standard, along with a document covering counterfeit-related defects and a risk assessment methodology and another one that expands the scope to cover higher-level assemblies containing electronics. The working group developing a standard for the detection of counterfeit assemblies is chaired by Dr. Diganta Das.
Standards play a crucial role in the smooth functioning and progress of the electronics industry. Standards can set clear guidelines and specifications for components, manufacturing processes, and finished products, helping achieve a consistent level of quality and reliability across the industry. Standards can also ensure that electronics meet safety requirements, minimizing the risk of malfunctions or accidents. Standards establish benchmarks for performance, safety, or other key metrics. Standards promote compatibility between components and devices made by different manufacturers. Because of the standards, you can use a charger from one brand with a phone from another without worrying about functionality. It enables companies to collaborate and source parts from various parts of the world, fostering innovation and efficiency. Standards create a common language and set of expectations within the electronics industry.
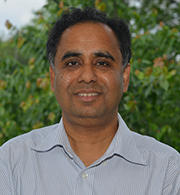
Dr. Diganta Das
For more information or questions regarding the standards or guidelines and to contribute knowledge and research, contact Associate Research Scientist and Associate Research Scientist Dr. Diganta Das.
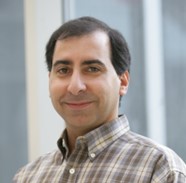
Dr. Michael Azarion
For more information or questions regarding the latest research findings and academic ideas in industry standards, contact the Research Scientist, Dr. Michael Azarian.
Top